Ever felt like your busbar bending machine is throwing a tantrum? Maybe it’s making weird noises, or the bends aren’t coming out right. It’s like having a car that won't start—frustrating and inconvenient. But don’t worry! Just like a car mechanic can diagnose and fix issues with your vehicle, understanding how to troubleshoot common problems with your busbar bending machine can save you time and hassle. Watch More to get expert solutions and keep your machine running smoothly.
Table of Contents
Sr# |
Headings |
1 |
Understanding Your Busbar Bending Machine |
2 |
Common Problems and Their Causes |
3 |
Issue 1: Uneven Bends |
4 |
Issue 2: Machine Not Starting |
5 |
Issue 3: Excessive Noise |
6 |
Issue 4: Inconsistent Measurements |
7 |
Issue 5: Difficulty in Adjustments |
8 |
Issue 6: Overheating |
9 |
Preventive Maintenance Tips |
10 |
When to Seek Professional Help |
11 |
Using the Manufacturer's Support Resources |
12 |
Upgrading Your Equipment |
13 |
Real-World Examples and Solutions |
14 |
Conclusion: Keeping Your Machine in Top Shape |
Understanding Your Busbar Bending Machine
Think of your busbar bending machine as a finely tuned instrument. Just like a piano needs to be in tune to sound right, your machine needs to be properly maintained and understood to work correctly. Knowing how your machine works is the first step in troubleshooting issues.
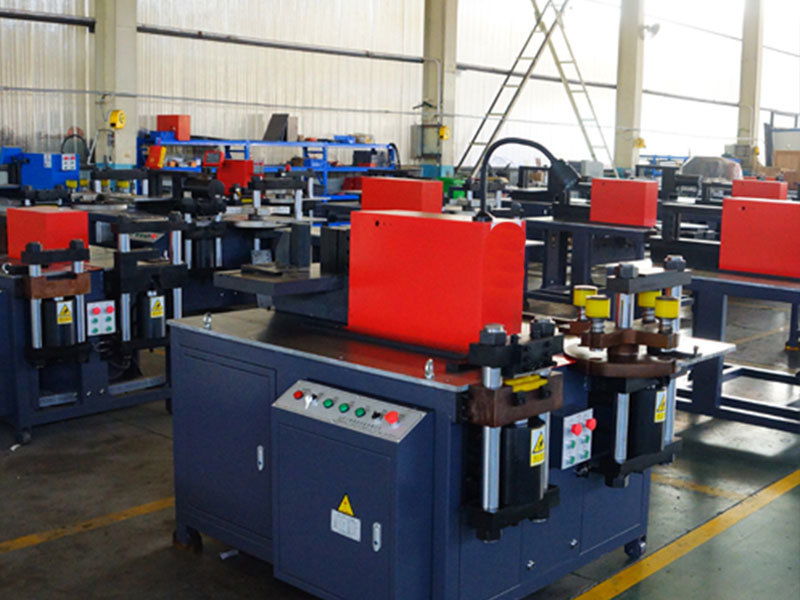
Common Problems and Their Causes
Busbar bending machines, like any complex equipment, can experience issues from time to time. Here’s a look at some common problems and what might be causing them:
- Uneven Bends
- Machine Not Starting
- Excessive Noise
- Inconsistent Measurements
- Difficulty in Adjustments
- Overheating
Issue 1: Uneven Bends
Uneven bends are like a cake that’s lopsided—it just doesn’t look right. This issue can be caused by:
- Incorrect Settings: Double-check that the machine settings match the specifications of your busbar.
- Misalignment: Ensure that the busbar is aligned correctly in the machine.
- Tool Wear: Worn or damaged tools can cause uneven bends. Regularly inspect and replace them as needed.
Solution:
- Recalibrate the Machine: Follow the manufacturer’s guidelines to recalibrate your machine.
- Check Alignment: Adjust the alignment settings to ensure even bends.
- Replace Worn Tools: Use fresh, high-quality tools to avoid deformation.
Issue 2: Machine Not Starting
If your machine won’t start, it’s like your car’s engine refusing to turn over—frustrating and often a sign of underlying issues. Possible causes include:
- Power Supply Issues: Check if the machine is properly plugged in and receiving power.
- Fuse Problems: A blown fuse can prevent the machine from starting.
- Emergency Stop Activated: Ensure that the emergency stop button isn’t engaged.
Solution:
- Inspect the Power Supply: Confirm that the machine is correctly connected and that the power source is functioning.
- Replace Fuses: If the fuse is blown, replace it with one of the correct rating.
- Reset Emergency Stop: Deactivate the emergency stop button if it’s engaged.
Issue 3: Excessive Noise
Excessive noise from your machine can be alarming, similar to a car making strange sounds. This can be caused by:
- Loose Components: Check for any loose or improperly secured parts.
- Lack of Lubrication: Insufficient lubrication can cause increased friction and noise.
- Worn Bearings: Worn or damaged bearings can contribute to unusual sounds.
Solution:
- Tighten Components: Secure any loose parts to reduce noise.
- Lubricate Moving Parts: Apply lubricant to reduce friction and noise.
- Replace Bearings: Inspect and replace any worn bearings.
Issue 4: Inconsistent Measurements
Inconsistent measurements can be compared to baking a recipe with inaccurate measurements—it can lead to poor results. This issue may be caused by:
- Calibration Errors: The machine might need recalibration.
- Measurement Tool Issues: Check if the measurement tools are functioning correctly.
- Operator Error: Ensure that measurements are being taken correctly and consistently.
Solution:
- Recalibrate the Machine: Follow the instructions to recalibrate and ensure accurate measurements.
- Check Tools: Inspect measurement tools for accuracy and replace if necessary.
- Train Operators: Provide additional training to ensure consistent measurement practices.
Issue 5: Difficulty in Adjustments
Difficulty in making adjustments can be likened to struggling with a stubborn lock—it just won’t cooperate. This can result from:
- Stiff Adjusters: If the adjusters are stiff, it can make adjustments challenging.
- Incorrect Settings: Ensure that the settings are properly configured for the task.
- Mechanical Issues: Check for any mechanical issues that may be hindering adjustments.
Solution:
- Lubricate Adjusters: Apply lubricant to smooth out stiff adjusters.
- Verify Settings: Double-check and adjust the machine settings as needed.
- Inspect Mechanisms: Look for and fix any mechanical issues affecting adjustments.
Issue 6: Overheating
Overheating is like your car engine running too hot—it can lead to serious problems if not addressed. This can be caused by:
- Continuous Operation: Running the machine for extended periods without breaks can cause overheating.
- Cooling System Issues: Check if the cooling system is functioning properly.
- Blocked Vents: Ensure that vents are not blocked and allow proper airflow.
Solution:
- Take Breaks: Allow the machine to cool down between extended operations.
- Check Cooling System: Ensure that the cooling system is working efficiently.
- Clear Vents: Keep vents clear to allow for proper airflow and cooling.
Preventive Maintenance Tips
Preventive maintenance is like routine check-ups for your car—keeping your machine in top shape can prevent many issues:
- Regular Cleaning: Keep the machine clean to prevent debris buildup.
- Routine Inspections: Perform regular inspections to identify and address potential issues.
- Scheduled Maintenance: Follow the manufacturer’s recommended maintenance schedule.
When to Seek Professional Help
Sometimes, issues can be too complex or severe for DIY fixes. If you’re encountering persistent problems or significant damage, it’s time to seek professional help. They can provide expert diagnosis and repair to get your machine back in working order.
Using the Manufacturer's Support Resources
Manufacturers often provide valuable resources, including:
- User Manuals: Detailed guides on operation and troubleshooting.
- Customer Support: Access to professional support and advice.
- Training Materials: Educational resources for proper machine use and maintenance.
Upgrading Your Equipment
If you’re experiencing frequent issues or need advanced features, consider upgrading your equipment. Newer models may offer improved performance, enhanced capabilities, and better reliability.
Real-World Examples and Solutions
Understanding real-world examples can help you see how others have solved similar issues. For instance, businesses often share their experiences and solutions for common problems, providing practical insights and tips.
Conclusion: Keeping Your Machine in Top Shape
Troubleshooting busbar bending machines doesn’t have to be daunting. With the right knowledge and a proactive approach, you can resolve common issues and keep your machine running smoothly. Remember to follow preventive maintenance practices, seek professional help when needed, and utilize manufacturer resources for the best results.